登場人物
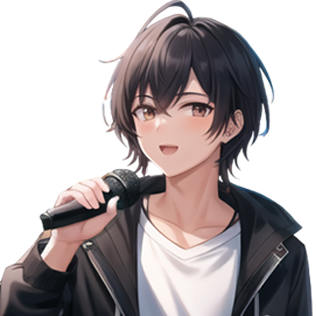
木村(司会)
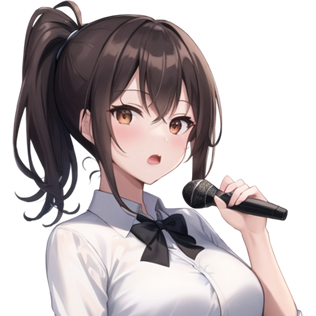
Airi(参加者)
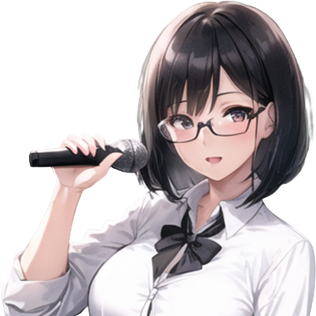
Erika(参加者)
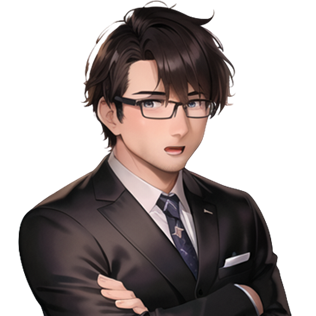
青木(審査員)
木村 皆さん、こんにちは。私は木村と申します。今日は「はんだごては効率的な製造プロセスの一環?」というテーマでディベートを行います。対戦者は「Airiさん」と「Erikaさん」です。まずはAiriさんから、肯定側の立論をお願いします。
Airi ありがとうございます、木村さん。はんだごては製造プロセスにおいて非常に効率的です。これは、電子機器の組み立て、配線の接続、修理作業など、幅広い分野で使用されており、高い信頼性と速さを提供しています。また、はんだごてを使えば、部品を確実に固定し、導電性を確保できます。これにより、品質向上と製造時間の短縮が実現します。
木村 では、Erikaさん、Airiさんの立論に対する反対尋問をお願いします。
Erika ありがとうございます。Airiさん、はんだごては確かに幅広い分野で使用されていますが、それにはコストもかかります。はんだごての材料やエネルギー消費についてどのように考えますか?そして、環境に与える影響についても教えていただけますか?
Airi それは重要な点ですね。はんだごては材料とエネルギーを必要としますが、効率的な製造プロセスを通じて、部品の確実な固定や導電性の確保に貢献しています。また、最新のはんだごて技術はエネルギー効率向上に取り組んでおり、環境に与える影響を最小限に抑える努力が行われています。
Erika しかし、はんだごての廃棄物や使用済み材料は環境への負荷を増やす可能性があります。再利用やリサイクルに関する取り組みはどうでしょうか?
Airi 確かに廃棄物や使用済み材料の管理は重要です。多くの企業はリサイクルプログラムを導入し、材料の再利用に努力しています。また、環境に配慮したはんだ材料の研究も進行中です。これにより、環境への負荷を減少させる方向に向かっています。
木村 それでは、Erikaさん、肯定側の立論に対する否定側の立論をお願いします。
Erika はんだごてが効率的な製造プロセスの一環であるという主張に対して、私は異議を唱えます。まず、はんだごてには欠点も存在します。例えば、高温で作業を行うため、作業者の安全に対するリスクが高まります。また、はんだ材料自体が有害な物質を含むこともあり、健康への悪影響が懸念されます。
さらに、はんだごては自動化が難しく、労力を必要とします。ロボット化や自動化が進んでいる現代において、労働力の効率的な利用を妨げる要因となり得ます。この点において、はんだごては製造プロセスの効率性を制約していると言えるでしょう。
また、はんだごては環境にも負荷をかけます。高温での作業によるエネルギー消費や廃棄物の処理が課題となります。環境への影響を最小限に抑えるためには、はんだごて以外の方法を模索すべきです。
これらの点から、はんだごては効率的な製造プロセスの一環ではないと結論いたします。
木村 それでは、Airiさん、Erikaさんの立論に対する反対尋問をお願いします。
Airi Erikaさん、はんだごての高温作業に関しては確かに作業者の安全が懸念されますが、近年では安全対策が進歩しています。作業者に対する適切な防護装備や訓練が行われ、リスクを最小限に抑える取り組みが増えています。これについてどうお考えですか?
Erika 確かに安全対策の向上は重要ですが、それでも高温作業自体が健康への悪影響を持つ可能性があることに変わりはありません。防護装備や訓練に頼るのではなく、より安全な製造プロセスの採用を検討するべきだと考えます。
Airi 環境への負荷についても、はんだごて技術の進歩により、エネルギー効率が向上しています。また、廃棄物のリサイクルや環境に配慮した材料の開発が進行中です。これにより、環境への影響を軽減する努力が行われています。この点についてどうお考えですか?
Erika 環境への取り組みは評価できますが、それでもはんだごて自体が他の製造方法に比べてエネルギーを多く消費し、廃棄物を発生させます。より持続可能な方法を模索すべきだと考えます。
木村 それでは、Erikaさん、Airiさんの反対尋問に対する反駁をお願いします。
Erika Airiさん、はんだごての安全対策の進歩についてお話しましたが、高温作業による作業者の健康への悪影響を完全に排除することは難しいと考えます。例えば、長時間の高温作業による熱中症のリスクはどのように克服できると思いますか?
Airi 確かに長時間の高温作業は熱中症のリスクを増加させる可能性があります。そのため、労働時間や作業環境の調整が必要です。作業者の休憩や水分摂取の確保、効果的な冷却装置の導入など、安全対策を継続的に強化することでリスクを最小限に抑える努力が求められます。
Erika しかし、それでも高温作業は作業者のストレスや疲労を引き起こし、生産性の低下につながることがあります。この点についてはどうお考えですか?
Airi 確かに高温作業はストレスや疲労を引き起こす可能性がありますが、効率的な製造プロセスとしてはんだごての利点は生産性向上に寄与しています。高品質な製品を短時間で生産できることを考えれば、そのメリットが大きいと言えます。
木村 では、Airiさん、Erikaさんの反駁をお願いします。
Airi Erikaさん、高温作業に関するリスクや生産性の低下についておっしゃりましたが、はんだごて技術は常に進化しています。例えば、無鉛はんだの普及により、有害物質の使用が減少し、作業環境が改善されています。また、ロボットを活用した自動化が進行中で、労働者の負担を軽減し、生産性向上に寄与しています。このような進展についてどのように見ますか?
Erika 確かに無鉛はんだや自動化の進展はポジティブな点ですが、それでも高温作業に依存する限り、リスクや労働者の負担を完全に排除することは難しいでしょう。また、自動化が進んでいるにも関わらず、作業者のスキルや監督が必要です。それに対するコストも考慮すべきです。
Airi 確かにコスト面や労働者のスキルは重要な要素ですが、はんだごてを使った製造プロセスの高い信頼性や品質についてはどうお考えですか?
Erika 品質の面では、はんだごては高い信頼性を持つことがあると認めますが、それでも新たな技術やプロセスの開発により、同様の品質を維持しつつ環境や労働者の健康に配慮できる方法を模索すべきだと思います。
木村 それでは、Erikaさん、最終弁論をお願いします。
Erika はんだごては確かに一部の製造プロセスにおいて有用であることは認めますが、効率的な製造プロセスの一環としては適していないと考えます。高温作業による安全リスク、環境への負荷、生産性の制約などが考慮されるべきです。新たな技術とプロセスの導入により、より持続可能かつ効率的な製造プロセスを追求すべきです。この点において、はんだごては効率的な製造プロセスの一環ではないと結論いたします。
木村 次に、Airiさん、最終弁論をお願いします。
Airi はんだごては確かに一部の課題を抱えていますが、効率的な製造プロセスの一環であると考えます。高品質な製品を生産し、信頼性を確保できることは大きなメリットです。また、新たな技術や安全対策の進歩により、リスクを最小限に抑え、環境に配慮しつつも利点を享受できるのです。
はんだごては製造業界において不可欠なツールであり、その存在感は変わりません。効率的な製造プロセスに欠かせない一環として、はんだごての価値は続きます。
木村 では、ジャッジ青木さん、どちらの主張がディベートに勝利したか、判定をお願いします。
ジャッジ青木 ディベートをじっくりと聞いた結果、両者の主張には一定の根拠があり、重要な観点が提示されました。しかし、最終的には肯定側のAiriさんの主張がより説得力があり、はんだごてが効率的な製造プロセスの一環であるという立場が優位に立ちました。彼女は高品質な製品、信頼性の確保、技術の進化、環境への配慮といった点で有益な側面を強調しました。
一方、否定側のErikaさんも一部のリスクや課題を指摘しましたが、それらの点が完全にはんだごての利点を覆すほどの重要性を持たなかったと判断いたします。
したがって、肯定側のAiriさんの主張が優勢であると判定します。
木村 Airiさん、Erikaさん、素晴らしいディベートをありがとうございました。お二人は熱心に議論を行い、それぞれの立場を説得力を持って表現されました。このディベートは非常に興味深く、示唆に富んだものでした。
Airiさん、あなたははんだごての利点を明確に説明し、効率的な製造プロセスの一環としての重要性を示しました。説得力のある主張を提示しましたね。
Erikaさん、逆説的な視点からはんだごての課題を指摘し、環境や安全面に焦点を当てました。あなたの立場も非常に重要な観点を示していました。
両者の対立する意見が、より良い理解と議論を促進しました。お二人の熱意と知識に感銘を受けました。
このディベートを通じて、新たな視点や洞察を得ることができました。次回もまた、刺激的なディベートを行いましょう。ありがとうございました。
ディベートを締めくくります。「はんだごては効率的な製造プロセスの一環?」についての議論はここで終了となります。お疲れ様でした。
コメント